Advanced Testing Procedures
Our advanced testing procedures guarantee that each product undergoes thorough quality checks to maintain consistency and meet industry benchmarks.
Continuous Improvement
Through continuous improvement initiatives, we aim to enhance our processes and constantly raise the bar for quality assurance in production.
Traceability and Transparency
Our transparent and traceable production process ensures accountability and allows for detailed tracking of each product through its journey from creation to distribution.
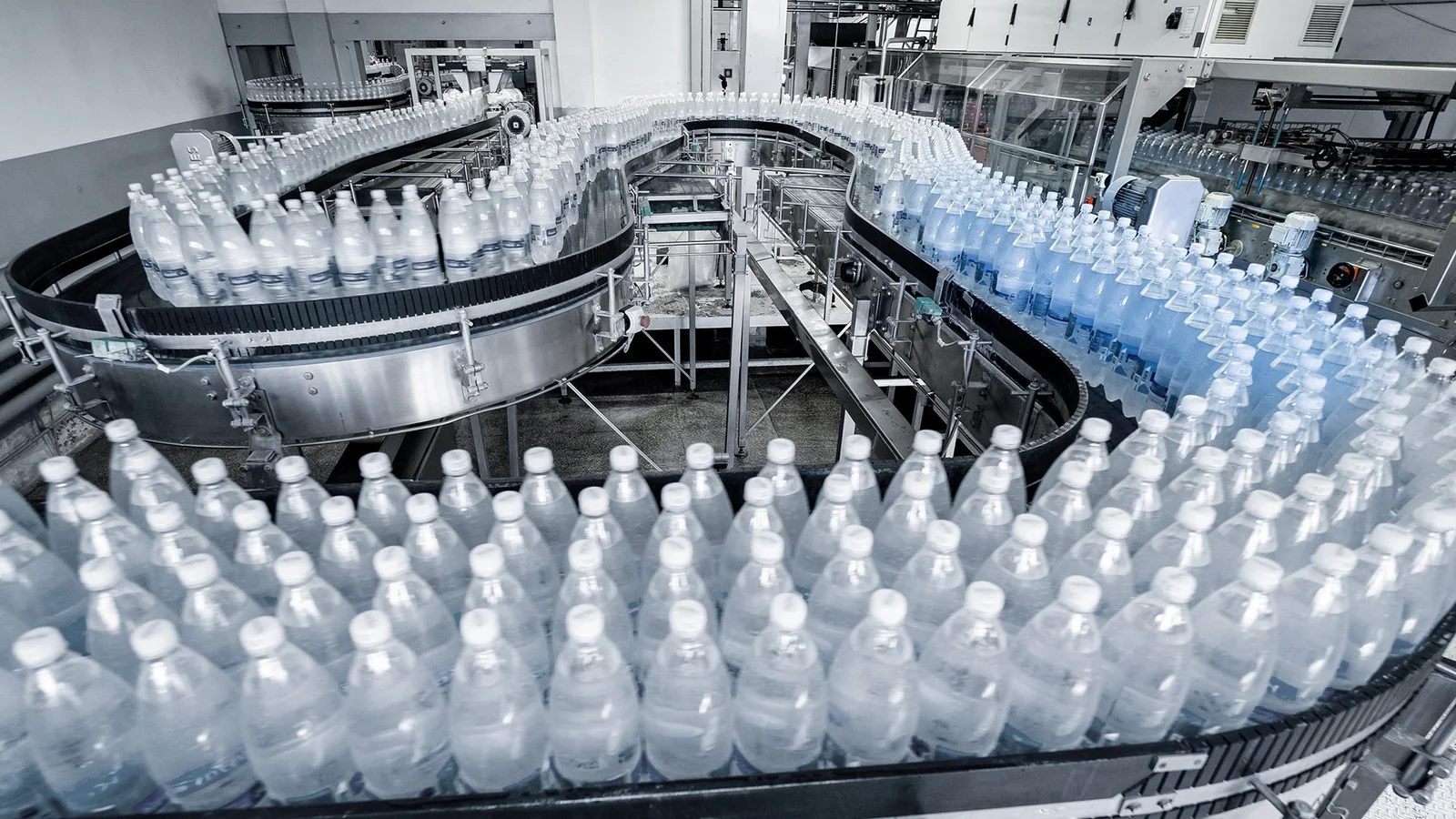
Maximizing Efficiency Through Integrated Solutions
Our integrated approach combines cutting-edge technology and expert craftsmanship to optimize efficiency and streamline your production process. Experience unparalleled performance and reliability with our comprehensive solutions.
Advanced Testing Procedures
Our advanced testing procedures guarantee that each product undergoes thorough quality checks to maintain consistency and meet industry benchmarks
Quality Assurance
Quality is at the core of everything we do. Our stringent quality assurance measures ensure that every product meets the highest standards of excellence.
Traceability and Transparency
With versatile and adaptable configurations, our solutions cater to your changing needs and evolving production requirements. Stay agile and responsive with our flexible setups.
Precision Solutions for Liquid Packing
COMPONENTS
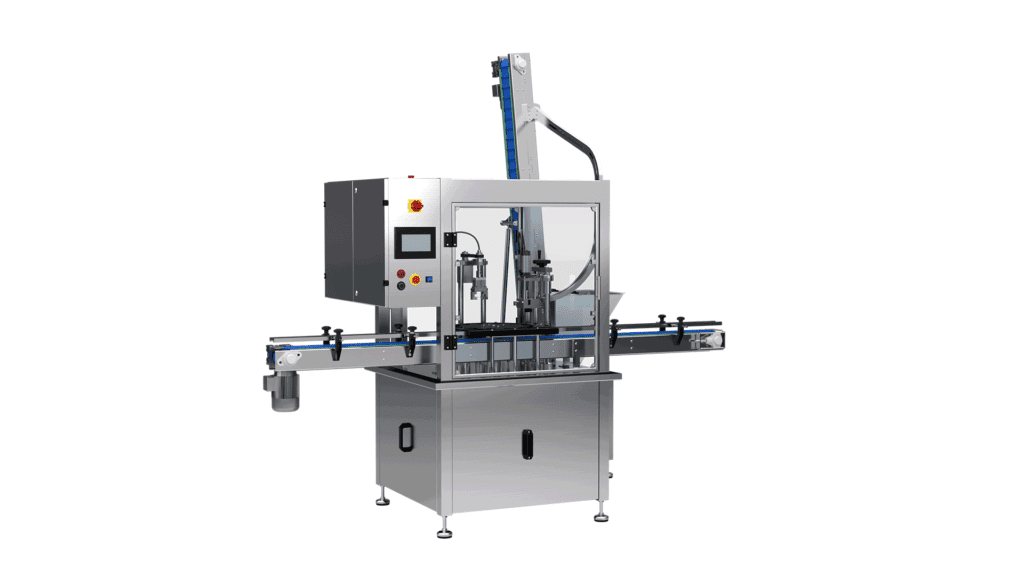
Rotary Capping Machine
A filling system that maximizes liquid filling capacity with a rotating structure and increases efficiency by accelerating your production processes.
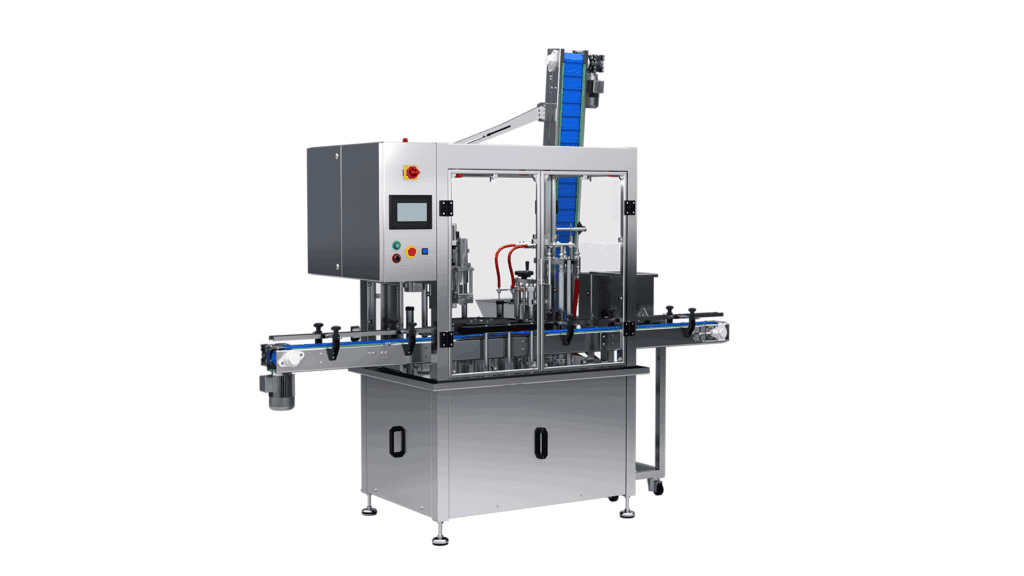
Rotary Filling and Capping Machine
A filling system that maximizes liquid filling capacity with a rotating structure and increases efficiency by accelerating your production processes.
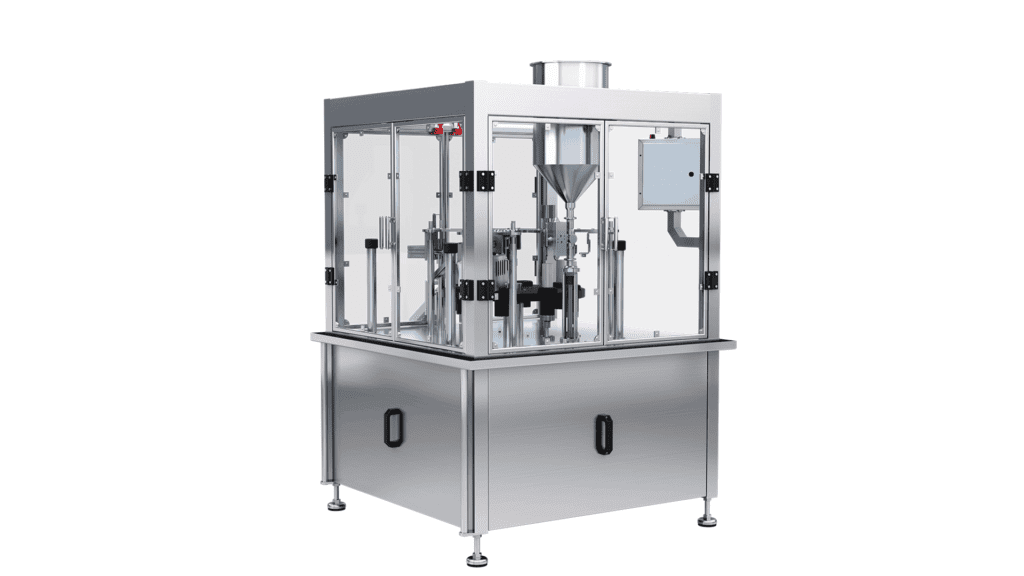
Tube Filling Machine
It is a machine that speeds up your filling processes and provides efficiency in your production line by filling tubes with high precision.
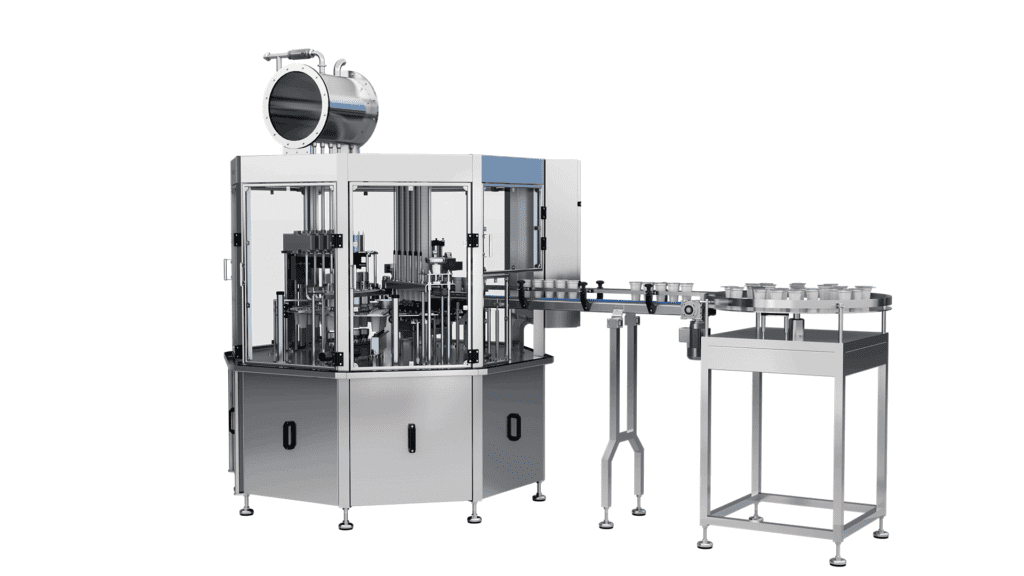
Sealing Machine
It is a machine that speeds up your production process by performing the closing process quickly and reliably with its rotary filling system.
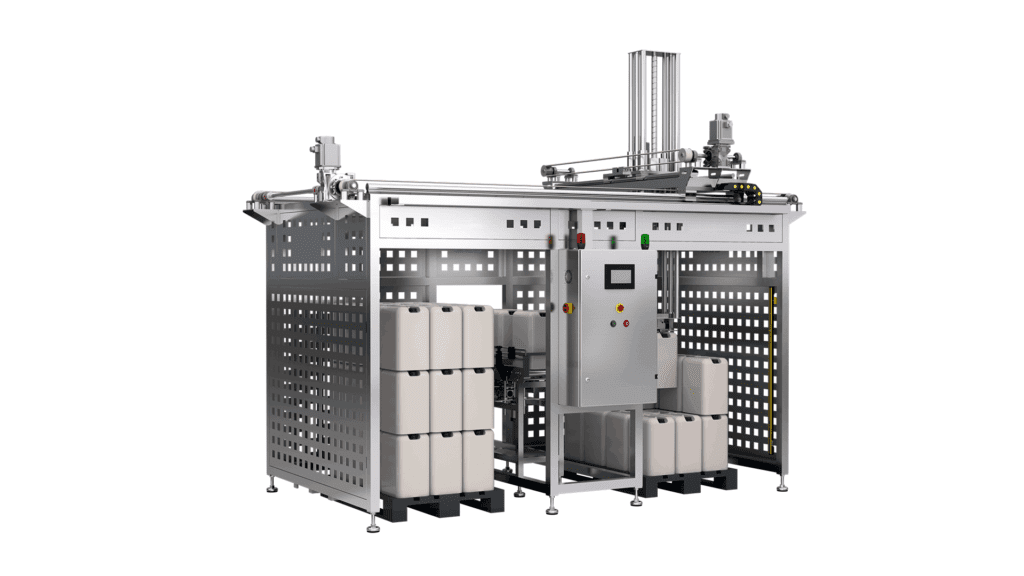
Automatic palleting Machine
It is a machine that facilitates storage and shipping processes by placing your products on pallets in an orderly and safe manner.
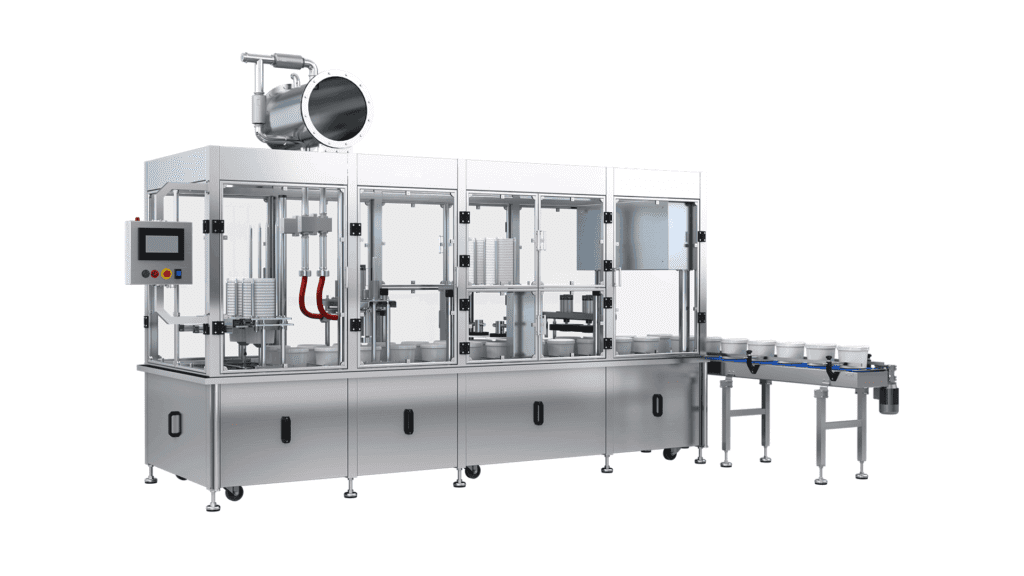
Bucket Filling Machine
A system that speeds up your production line by performing the filling and closing operations of buckets efficiently and safely.
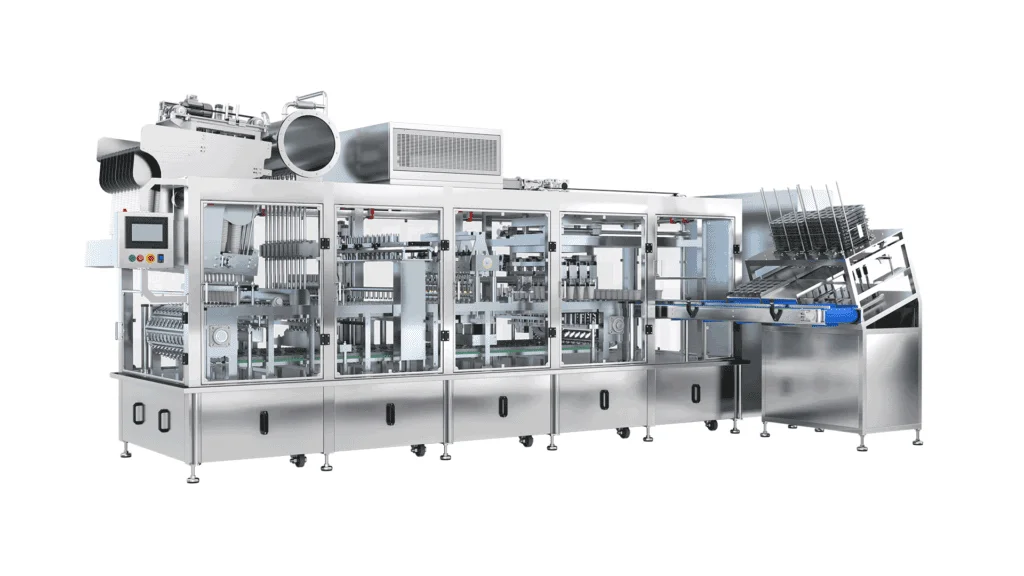
Filling and Sealing Machine
It is an integrated system that provides speed and reliability in the production line by combining liquid filling and capping processes.
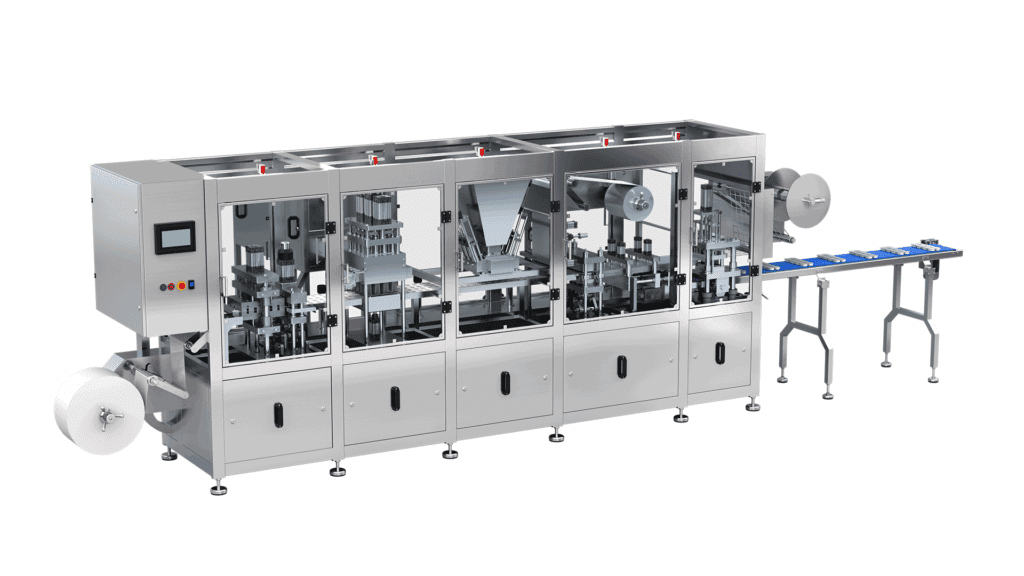
Thermoforming Machine
Automatic thermoforming machine that speeds up your packaging production processes and provides flexibility by thermoforming.
Filling, Capping & Labeling line Technical Specifications
FILLING | CAPPING | LABELLING | ||
---|---|---|---|---|
Volume | 20 cc – 20000 cc | 20 cc – 20000 cc | WxL mm | 20-160 x 300 |
Quantity | 200 pcs – 2400 pcs /h | 200 pcs – 2400 pcs/h | Coil Diameter | 300 mm |
Sensitivity | 0,5% | ———– | Output Speed | 20 m/min |
System | Electromagnetic Flow Meter (Endress+Houser), Volumetric or Load cell | Pick and place with gripper head, pneumatic motor or head with controlling mechanical torque | Number of labeling | Max 3000 pcs/h |
Roll diameter | 76 mm | |||
Nozzle System | Nozzle with Internal Closing | Module Motor | Stepper motor | |
Nozzle Quantity | 1 pcs – 12 pcs | |||
Working Pressure | 6-8 Bar | 6-8 Bar | ——— | |
Working Voltage | 380 Volt / 50 Hz | 380 Volt / 50 Hz | 220 volt / 50 Hz | |
Control Voltage | 24V DC | 24V DC | 24V DC | |
Control Unit | PLC | PLC | Coding unit | Optional |
Cabin | Plexyglass | Plexyglass | ———- | |
Product Sensor | Diffuse Optical Sensor | Diffuse Optical Sensor | Diffuse Optical Sensor | |
Conveyor system | Moduler band | Moduler band | Moduler band | |
Conveyor Motor | 380 Volt 0.37 kW | 380 Volt 0.37 kW | 380 Volt 0.37 kW | |
Electricity consumption | 4 KW | 1,5 KW | 1 KW | |
Conveyor Unit | AISI 304 Chassis with Moduler band | AISI 304 Chassis with Moduler band | AISI 304 Chassis with Moduler band | |
Conveyor Width | 82.5mm-165mm | 82.5mm-165mm | 82.5mm-165mm | |
Pneumatic materials | FESTO/SMC | FESTO/SMC | There is no label | Optional |
FILLING | CAPPING | LABELLING | ||
---|---|---|---|---|
Volume | 20 cc – 20000 cc | 20 cc – 20000 cc | WxL mm | 20-160 x 300 |
Quantity | 200 pcs – 2400 pcs /h | 200 pcs – 2400 pcs/h | Coil Diameter | 300 mm |
Sensitivity | 0,5% | ———– | Output Speed | 20 m/min |
System | Electromagnetic Flow Meter (Endress+Houser), Volumetric or Load cell | Pick and place with gripper head, pneumatic motor or head with controlling mechanical torque | Number of labeling | Max 3000 pcs/h |
Roll diameter | 76 mm | |||
Nozzle System | Nozzle with Internal Closing | Module Motor | Stepper motor | |
Nozzle Quantity | 1 pcs – 12 pcs | |||
Working Pressure | 6-8 Bar | 6-8 Bar | ——— | |
Working Voltage | 380 Volt / 50 Hz | 380 Volt / 50 Hz | 220 volt / 50 Hz | |
Control Voltage | 24V DC | 24V DC | 24V DC | |
Control Unit | PLC | PLC | Coding unit | Optional |
Cabin | Plexyglass | Plexyglass | ———- | |
Product Sensor | Diffuse Optical Sensor | Diffuse Optical Sensor | Diffuse Optical Sensor | |
Conveyor system | Moduler band | Moduler band | Moduler band | |
Conveyor Motor | 380 Volt 0.37 kW | 380 Volt 0.37 kW | 380 Volt 0.37 kW | |
Electricity consumption | 4 KW | 1,5 KW | 1 KW | |
Conveyor Unit | AISI 304 Chassis with Moduler band | AISI 304 Chassis with Moduler band | AISI 304 Chassis with Moduler band | |
Conveyor Width | 82.5mm-165mm | 82.5mm-165mm | 82.5mm-165mm | |
Pneumatic materials | FESTO/SMC | FESTO/SMC | There is no label | Optional |